TEXT ABOVE
Load indicators: the key to crane safety
Sure, accidents happen. But when it comes to heavy lifting and crane operations, accidents are no laughing matter. According to the U.S. Bureau of Labor Statistics, there were an average of more than 40 fatal crane accidents per year in the U.S. between 2011–2017. In fact, one-third of all worker deaths involve a crane, with more than half of all fatal crane injuries involving the worker being struck by an object or equipment.
There are many causes for crane accidents, and one of the most common also happens to be one of the easiest to prevent—overloads. By some estimates, 80 percent of all crane upsets and structural failures are a direct result of exceeding the crane’s operational capacity.
So what can be done? There are obvious steps like making sure operators are fully licensed and trained, have adequate supervision, and that the loads are properly balanced.
But there’s one more step that’s often overlooked—using a load indicator to prevent overloads.
Makes sense, right? If you use a digital load indicator, you’ll always know that your load doesn’t exceed the crane’s capacity.
What are load indicators?
As the name implies, a load indicator is a type of force gauge instrument that lets crane operators know the exact weight of the load being lifted. A load indicator is basically another name for crane scales or load cells, or more specifically, the part of the system that indicates or displays the lifted load’s weight. These systems use weight sensors to measure the amount of force or tension applied to them.
There are a few different types of loading indicators.
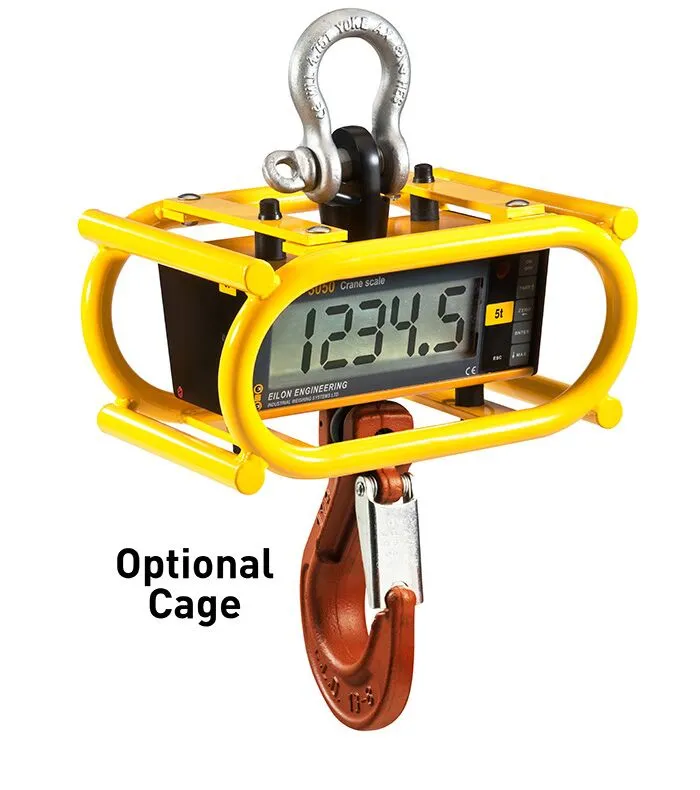
Integrated display
With this setup, the load indicator is built into the load cell or crane scale. This is fine for many types of applications where operators are close enough to the lifted load to read the display.
But for larger applications, you’ll likely need another solution.
Also, some applications might call for the addition of a protective cage to ensure the indicator isn’t damaged during the lift.
Finally, this setup also has the possible disadvantage of it being harder to execute certain operations on the indicator, such as tare, max, zero, etc., since the operator must be in close physical proximity to the lifted load in order to do so.
Not so with a remote load indicator.
Remote display
While safety is doubtlessly the number one concern, using a weighing system that includes a load indicator has several other benefits:
- Improved lifting efficiency: With accurate weight information, operators can conduct safe, precise lifts, minimizing risks while optimizing lifting speed and accuracy. This can lead to faster project completion and increased productivity.
- Improved decision-making: Load indicators empower operators to make informed decisions throughout the lifting process. They can adjust lifting angles, boom placement, and other factors based on the actual load weight, ensuring safe and controlled operations.
- Data logging and recording: Some advanced load indicators offer data logging and recording capabilities. This allows for post-lift analysis, helping to identify potential safety concerns and improve future operations.
- Enhanced operator confidence: Knowing the exact weight of the load provides operators with confidence and peace of mind during lifting operations. This can reduce stress and improve focus, leading to safer and more efficient work.
Load indicators: applications
Digital load indicators have a broad range of uses across many industries. Here are a few common uses:
- Overload prevention: Crane overloads are a major safety risk, even when the load’s weight is known. This is due to potential scenarios like equipment being anchored to the ground, poor communication between crew members, uneven load distribution, and more.
- Shipment weighing: This can help reduce costs by verifying supplier reports of incoming shipments, monitoring outgoing shipments, and more.
- Controlled cable tensioning: Controlled cable tensioning is the process of applying and maintaining a precise, desired force within a cable or wire for optimal performance and structural stability. This process uses specialized equipment including tension meters, a load indicator, cable grips, and more.
- Bollard pull tests: A bollard pull test measures the maximum pulling force (thrust) a vessel can exert against a fixed bollard to determine its towing and load-bearing capabilities. Here, a quality load indicator is necessary to read and record the results.

How to choose a load indicator
Finding the right load cell indicator for your needs might sound like a difficult process, but it doesn’t have to be.
First, choose a reputable company with a proven track record. After all, safety is always the top concern so you’ll want a system you can trust.
Next, you’ll need to decide on the maximum lifting capacity your application calls for.
Eilon Engineering offers force gauge weighing systems in a range of capacities: from 0.5 tons to 300 tons. Choose a capacity that will suit all of your potential lifting applications and never lift more than the max capacity.
Next, decide on the type of indicator: integrated, remote, or wireless.
Finally, consider the size of the screen you’ll need. If you choose an integrated display, then you’ll need to consider the distance between the operator and the lifted load. With a handheld remote indicator, you can choose a smaller screen size. Eilon indicators come in a variety of screen sizes of 0.5”, 1”, and 2” LCD screens.
Load indicators in a nutshell
When it comes to lifting heavy equipment in an industrial setting, safety should be rule number one. A quality digital load indicator is a simple way to greatly increase onsite safety and help prevent tragic crane accidents.
By allowing operators to know the exact weight of the lifted load, loading indicators help prevent overloads and save lives.
So get in touch today, and we’ll be happy to help you find the perfect system for your weighing and lifting needs.
Phone:
US/Canada/Int'l: 1-888-778-8064
UK: 0800 8620354
Email:
sales@eilon-engineering.com